«Открывают новые перспективы перед промышленностью»: специалист — о развитии металлической 3D-печати в России
Учёный из НИТУ МИСИС рассказал RT о плюсах металлической 3D-печати
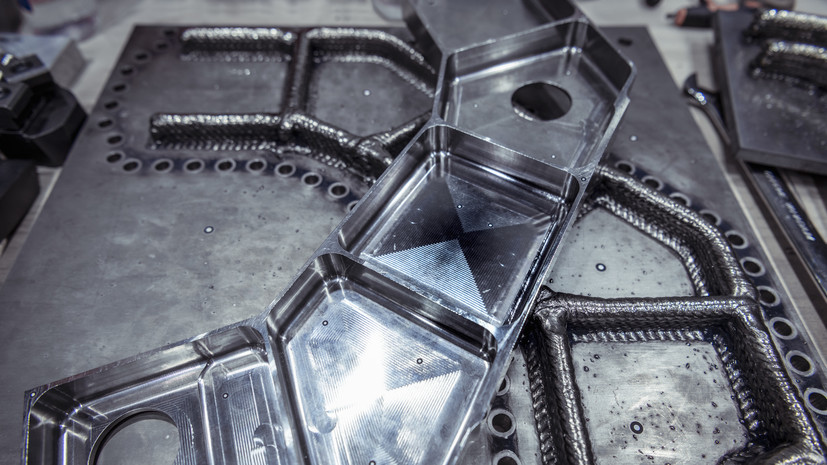
- Gettyimages.ru
— ГК «Росатом» разработала первый в России ГОСТ на производство порошков для 3D-печати из титановых сплавов. Сегодня 3D-печать набирает всё большую популярность, эту технологию даже называют будущим металлургии. Расскажите, пожалуйста, о ней подробнее.
— Начну с известного определения, что такое аддитивное производство. Это совокупность технологий создания трёхмерных физических объектов по данным исходных электронных моделей путём послойного добавления материала с использованием селективного подвода энергии — лазерного или электронного луча, электрической дуги и т. д. Электронная модель разрабатывается в виде 3D-изображения, при создании могут применяться данные рентгеновской томографии, например, если речь идёт о медицинской области.
Если говорить об аддитивных технологиях применительно к металлу, есть их следующие разновидности: селективное лазерное сплавление, когда металл сплавляется лазером; селективное электронно-лучевое сплавление; прямое лазерное выращивание — когда металл в виде порошка подаётся непосредственно в зону воздействия лазера. Рабочий инструмент при этом перемещается, что позволяет создавать сложные по форме и крупногабаритные объекты. Также есть селективное лазерное спекание, когда металлический или керамический порошок не плавится, а спекается. Применяется и электродуговая наплавка проволоки, когда в качестве прекурсора берётся не металлический порошок, а проволока, и технология струйного нанесения связующего для послойного склеивания, например, керамики с другими компонентами.
В зависимости от метода печати выбирается материал — это могут быть металлические порошки, проволоки, листы и т. д.
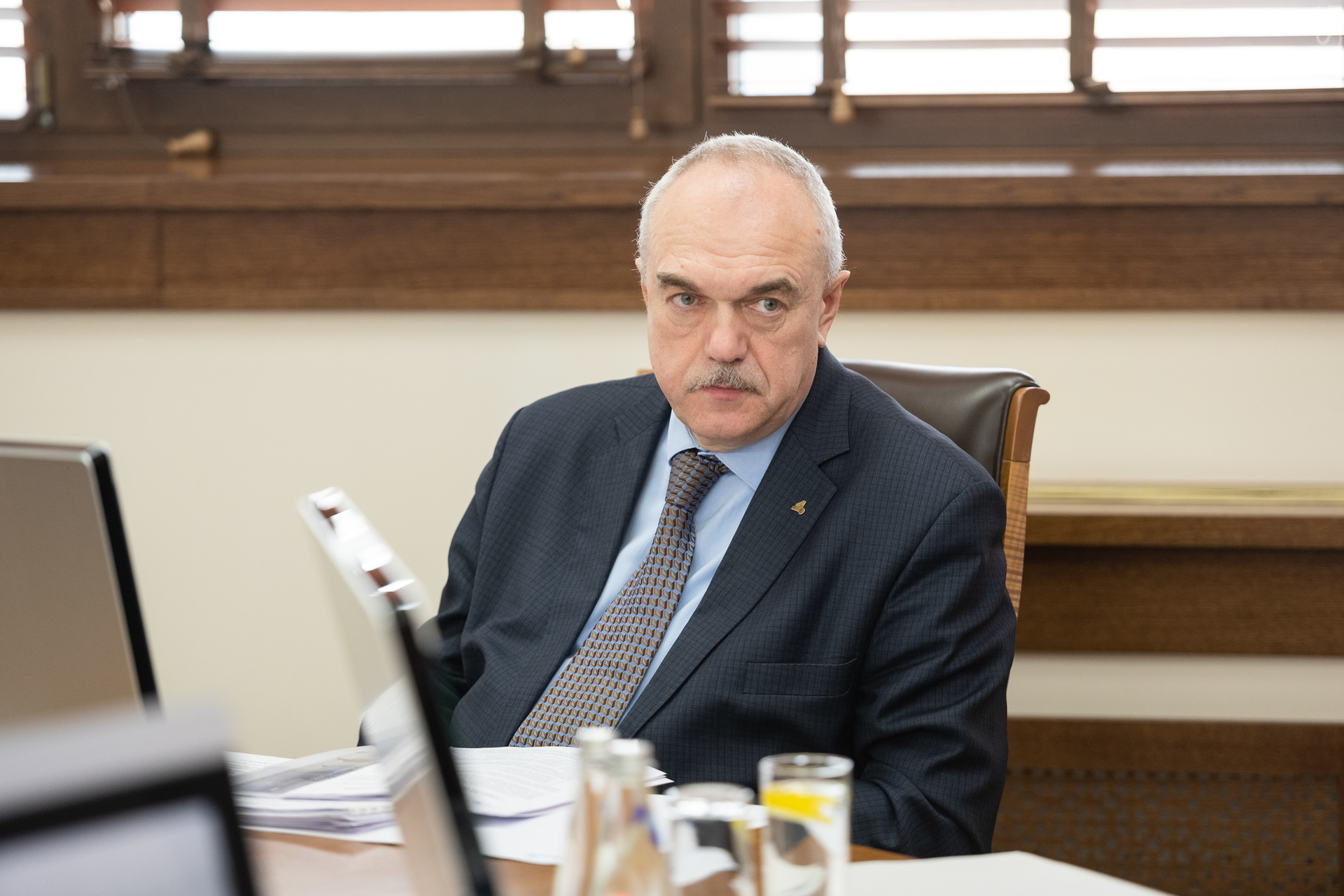
- Евгений Александрович Левашов
- © пресс-служба НИТУ МИСИС
— Почему на металлические порошки для 3D-печати требуются ГОСТы?
— Это исключительно актуальная тема. Мы начали беседу с новости о создании в России первого ГОСТа на производство титановых порошков, и это очень важно, например, для медицинской области. Титан, по сути, является одним из компонентов медицинских имплантатов, которые изготавливаются методом 3D-печати. Для их производства важно не допускать отклонений по химическому, гранулометрическому составу и морфологии порошков.
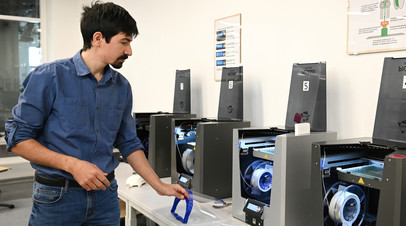
Это и призван обеспечить ГОСТ. При наличии стандартизированных металлических порошков аддитивные технологии могут активно применяться на базе даже отдельных клиник, не говоря о сетях медучреждений. Например, отделения ортопедии, травматологии, челюстно-лицевой хирургии на собственных установках 3D-печати могут изготавливать персонализированные имплантаты, что уже реализуется на практике. Но для этого нужен порошковый материал со стабильными свойствами и составом. Это также актуально для авиационно-космической отрасли, где действуют строгие стандарты по содержанию примесей, структуры и морфологии порошков. От этого зависят тактико-технические характеристики готового изделия.
— Отличаются ли физико-технические свойства напечатанных деталей, например, от литых металлических изделий?
— Конечно, отличаются — и пофункциональным, и по физико-механическим свойствам. В случае 3D-печати обработка металла осуществляется намного быстрее, чем в традиционной металлургии. Происходит достаточно быстрый переплав, спекание и быстрое охлаждение, кристаллизация. В результате формируется ультрамелкозернистая структура. Для сравнения: при традиционных технологиях литья, когда металл медленно нагревается и медленно остывает, в процессе успевает вырасти зерно, достигающее сотен микрон и миллиметров. Аддитивные же технологии позволяют получать субмикронные структуры.
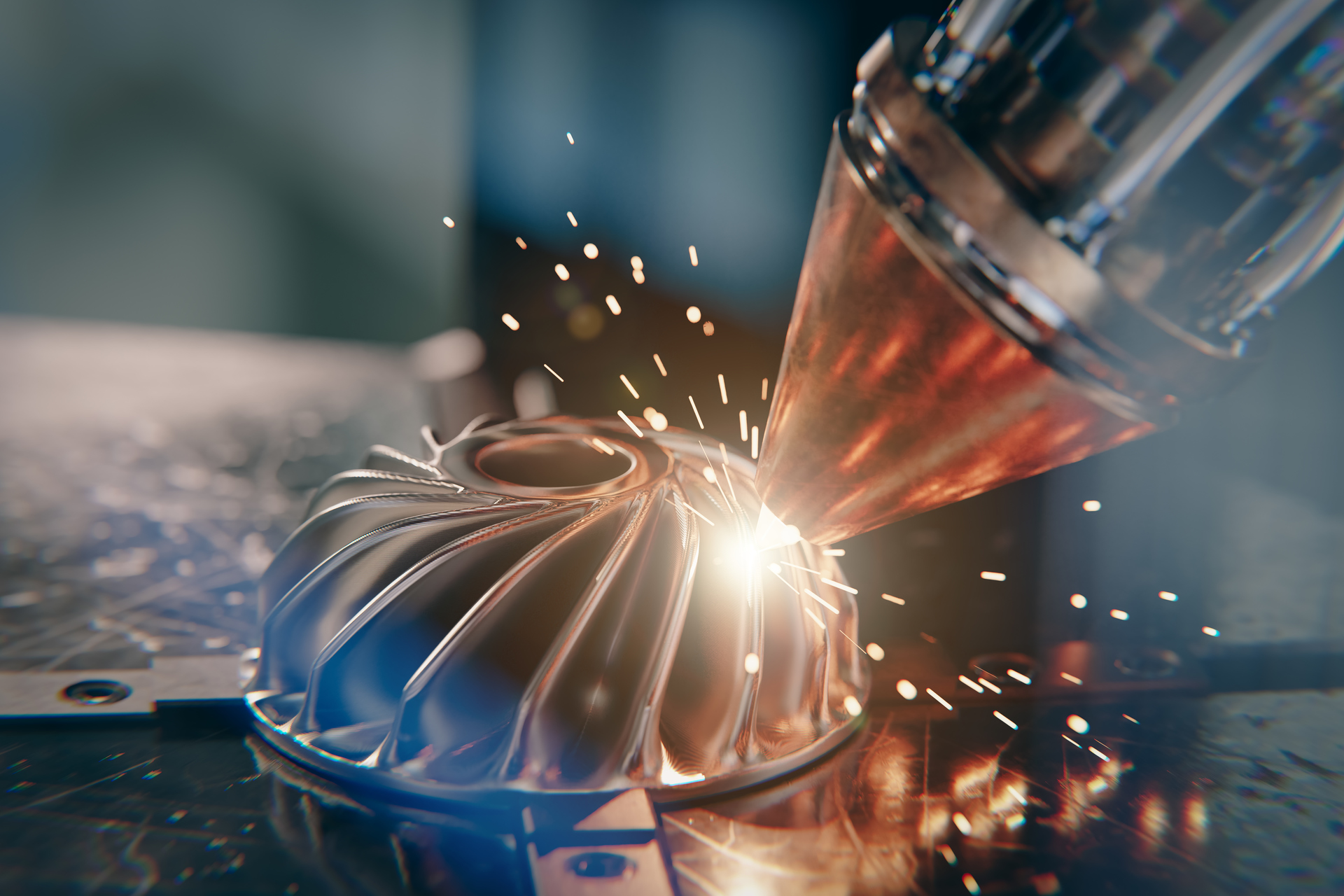
- Gettyimages.ru
— Такие материалы более прочны?
— Не всегда. Дело в том, что быстрое охлаждение металла, о котором мы говорили ранее, приводит к высоким внутренним напряжениям. Естественно, это означает, что такие материалы более хрупкие, обладают анизотропией структуры и свойств, то есть когда внутри материала присутствует неоднородность физических свойств. Также такой материал может содержать дефекты — непропечённые участки, поры, микротрещины.
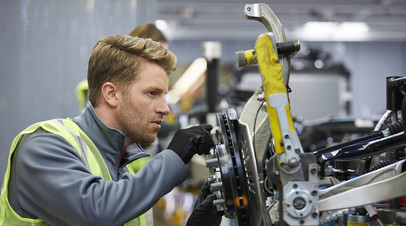
Поэтому полученный с помощью 3D-печати объект требует дополнительной постобработки. Она включает как минимум две операции. Во-первых, если требуется получить плотное, беспористое изделие, проводят горячее изостатические прессование, при котором «залечиваются» микропоры и трещины. Также дополнительно проводят термообработку — в металлургии это называется закалкой с последующим старением. Это позволяет снять напряжение, о котором я говорил ранее, и обеспечить дисперсное упрочнение. Иногда требуется и механическая обработка. Если 3D-технология не обеспечивает высокую точность соответствия электронной модели детали, то заготовку доводят с помощью фрезеровки и шлифовки.
— Какие преимущества даёт технология 3D-печати?
— Их много. Во-первых,возможность топологической оптимизации конструкции детали. Это означает, что можно одну и ту же геометрию, один и тот же функционал получить путём построения различных топологий. Во-вторых, снижение трудоёмкости производства, повышение надёжности деталей. И что очень важно, минимизация потерь и отходов, которые являются неотъемлемой частью традиционной металлургии — в виде стружки, абразива, литейного брака и т. д. Аддитивные технологии также позволяют изготавливать детали сложной геометрии с характеристиками, недостижимыми для традиционных технологий производства. Ну и мелкозернистая структура материала, о чём говорилось выше, тоже обеспечивает высокое качество деталей: после постобработки они отличаются высокой прочностью и сопротивлением деформации, в том числе при высоких температурах. Поэтому при использовании одного и того же сплава 3D-печать позволяет получить более высокие физико-механические свойства, чем традиционные технологии, иногда в полтора-два раза.
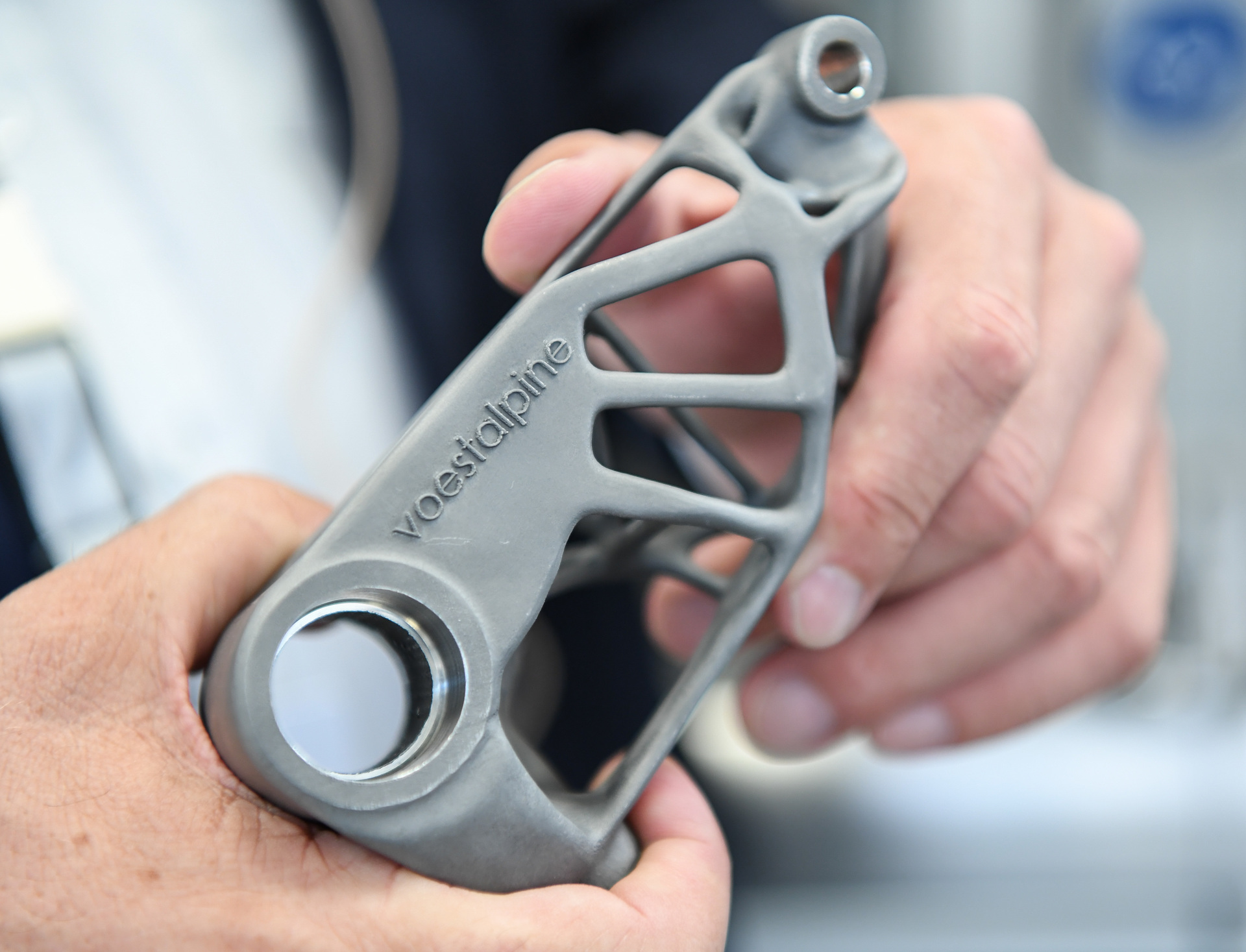
- © Wolfram Kastl/picture alliance via Getty Images
— Какое базовое образование нужно специалистам по 3D-печати по металлам? Достаточно ли в России таких специалистов сегодня?
— Для работы в сфере аддитивных технологий специалист должен обладать комплексными знаниями. Во-первых, он должен уметь управлять этой техникой — по сути, это ЧПУ более высокого уровня. А также обладать знаниями в IT-сфере, чтобы уметь строить электронные модели. Инженер, обслуживающий установку 3D-печати, должен иметь знания в области материаловедения, понимать, каким образом режимы печати могут повлиять на структуру и свойства материала.
Таких специалистов пока мало, по крайней мере явно меньше, чем требуется. Поэтому государство создаёт и поддерживает несколько передовых инженерных школ (ПИШ) в области аддитивных технологий, включая ПИШ «Материаловедение, аддитивные и сквозные технологии» НИТУ МИСИС.
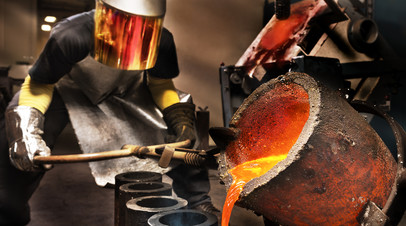
Сегодня Россия в чём-то даже опережает западные страны, если говорить об аддитивных технологиях: в стране разрабатываются уникальные материалы для различных отраслей промышленности. Однако в оборудовании не будет смысла, если на нём некому работать, поэтому подготовка кадров не должна отставать от развития станкостроения и электроники.
— Производится ли в России оборудование для металлической 3D-печати? Есть ли компетенции и мощности, чтобы расширить выпуск такого оборудования?
— Такое оборудование выпускается, причём уже серийно. Этим занимаются, в частности, ГК «Росатом», а также ряд малых и средних компаний. На российском рынке представлена целая линейка отечественных комплексов для 3D-печати. Да, есть проблемы с комплектующими, но и они со временем будут решены.
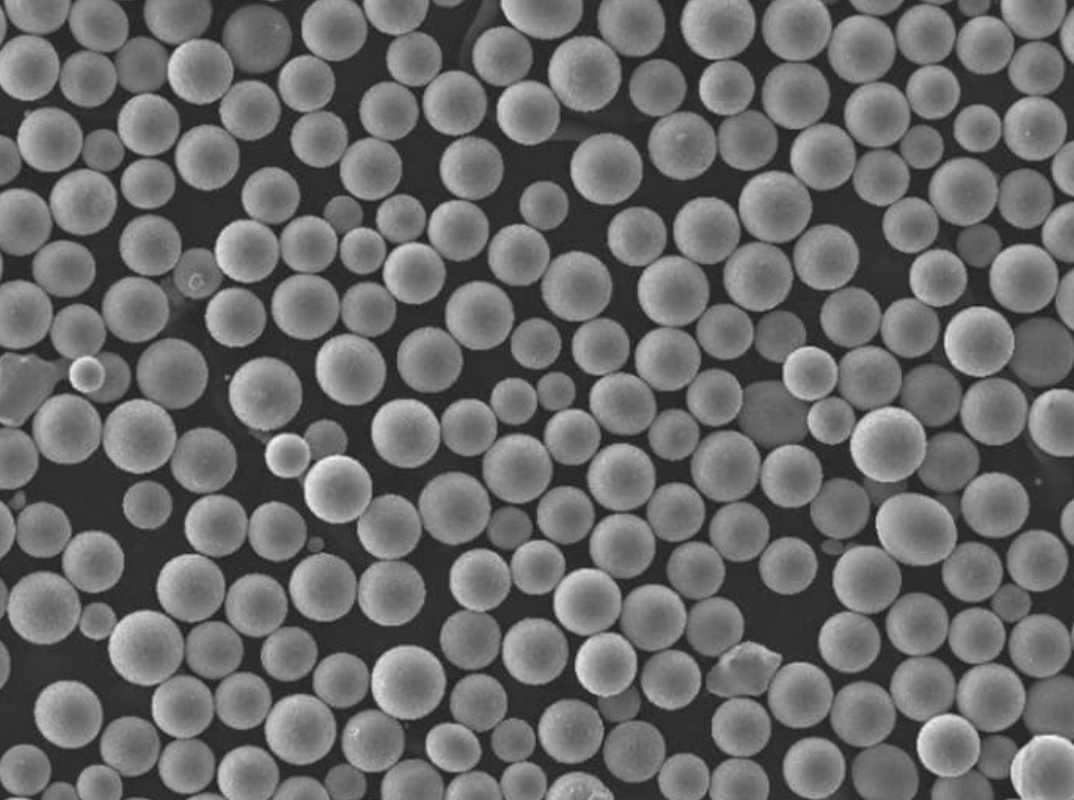
- Порошок для 3D-печати крупным планом
- © am-material.com
— Какие требования предъявляются к порошкам для 3D-печати? Производятся ли они в России?
— Все частицы в таком порошке должны иметь сферическую или округлую форму, регламентированный гранулометрический состав, минимальное количество сателлитов (дефектов. — RT) на поверхности. Также частицы должны иметь низкий уровень газовой пористости, низкий уровень газовых и газообразующих примесей, высокие физико-технологические свойства, однородный химический состав.
Есть ряд методов получения таких порошков. Газовое распыление металла, расплавленного в вакуумной камере путём индукционного нагрева (в тигле), или индукционная плавка электрода, совмещённая с распылением расплава газом.
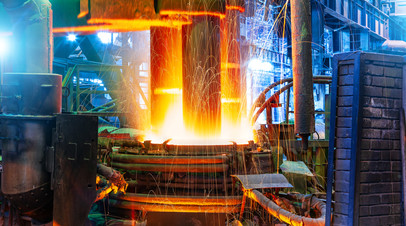
Хорошо развита и отечественная технология центробежной атомизации: распыление расплава, создаваемого электрической дугой между прутком материала и вольфрамовым электродом. А также технология распыления расплава с торца прутковой заготовки, создаваемого высокоскоростным потоком ионизированного инертного газа. Этот метод даёт самые высококачественные порошки.
Ещё один метод — сфероидизация узкофракционных порошков с неправильной формой частиц путём их обработки в потоке термической плазмы при использовании электродуговых или высокочастотных плазматронов. При этом поток порошка пропускают через высокотемпературную плазму, где песчинки оплавляются и становятся шариками. Такие установки разрабатываются, изготавливаются и уже применяются в России.
— 3D-печать — достаточно сложный и дорогостоящий процесс. О его технических преимуществах вы рассказали. А как обстоит дело с экономической окупаемостью, насколько выгодно бизнесу развивать это направление?
— Да, узкофракционные сферические порошки металлов и их сплавов для аддитивных технологий существенно дороже обычных порошков, недёшево стоят и сами установки для 3D-печати. Но в итоге их применение всё равно окупается — хотя бы за счёт улучшенных технических характеристик изделий и отсутствия побочных отходов производства. Поэтому аддитивные технологии открывают новые перспективы перед промышленностью, хотя и не призваны полностью заменить традиционную металлургию. Это и не нужно.
- Тоньше волоса: российские учёные напечатали 3D-детали из вольфрама с толщиной стенок 100 микрометров
- «Успешно движемся вперёд»: российские учёные напечатали на 3D-принтере магниты сложной формы с улучшенными свойствами
- В Ижевске открыли первый в России Центр аддитивных технологий общего доступа
- Высокая энергоэффективность: российские учёные создали структуры для новой электроники — магноники
- «Придаёт новые свойства приборам»: российские химики создали невидимое для тепловизоров керамическое покрытие